Guaranteed
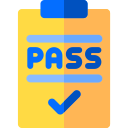
95.5% Pass Rate
CPA
Intermediate Leval
Management accounting November 2018
Suggested Solutions
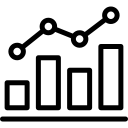
Management accounting
Revision Kit
Revision Kit